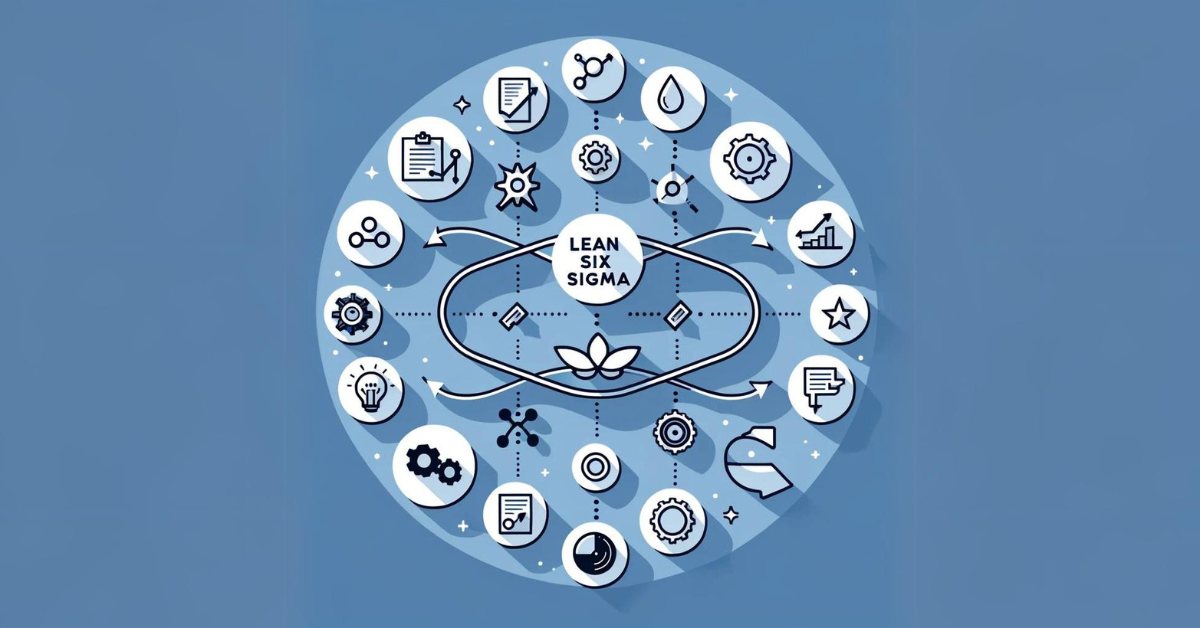
Lean Six Sigma: Sinergizando Eficiência e Qualidade
Lean Six Sigma representa uma fusão de duas metodologias poderosas de melhoria de processos: Lean, que se concentra na redução de desperdício e eficiência, e Six Sigma, que visa a qualidade e precisão ao eliminar defeitos. Quando combinados, eles formam uma abordagem abrangente para a excelência operacional.
Maximizando a Eficiência: O Impacto da Filosofia Lean nas Práticas Modernas de Negócios
A filosofia Lean é uma abordagem sistemática para identificar e eliminar o desperdício por meio da melhoria contínua, fundamentada no Sistema de Produção Toyota (TPS) do meio do século 20. O conceito está enraizado em definir valor a partir da perspectiva do cliente e garantir que a criação de valor ocorra com o mínimo de desperdício.
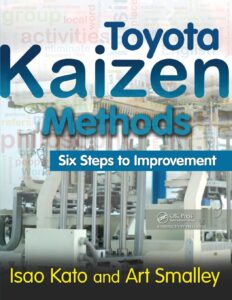
Esta filosofia teve origem nas operações de manufatura eficientes da Toyota, que estabeleceu princípios voltados para a eliminação de desperdício e o aprimoramento dos processos de produção.
Henry Ford é frequentemente citado como um dos primeiros contribuintes para a mentalidade Lean com seu sistema de produção em fluxo em Highland Park, que enfatizava o trabalho padronizado e o transporte em movimento para maximizar a eficiência. No entanto, foram os engenheiros da Toyota, principalmente Taiichi Ohno e Shigeo Shingo, que desenvolveram essas ideias no mais abrangente TPS na era pós-Segunda Guerra Mundial.
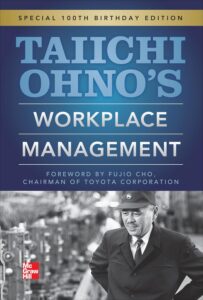
O sistema da Toyota foi construído com base nos princípios de gestão de estoque just-in-time e controle de qualidade automatizado, visando alcançar um fluxo harmonioso no processo de produção enquanto abraça uma filosofia de melhoria contínua.
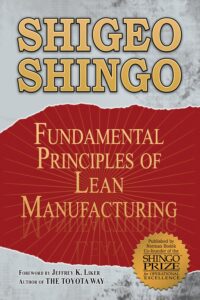
O termo ‘Lean’ em si foi criado muito depois, em 1988, por John Krafcik, e foi posteriormente definido e popularizado no livro ‘A Máquina que Mudou o Mundo’ por James P. Womack, Daniel T. Jones e Daniel Roos. Eles delinearam os princípios fundamentais do Lean como valor, fluxo, fluxo, puxada e perfeição, cada um desempenhando um papel crucial na redução de desperdício e melhoria da produtividade.
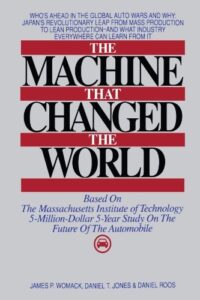
Hoje, a filosofia Lean é aplicada não apenas na indústria, mas também em vários setores, como saúde, desenvolvimento de software, educação e outros.
Empresas de diferentes indústrias utilizam estratégias Lean para aumentar a eficiência, reduzir o desperdício e melhorar a produtividade geral. Por exemplo, a Toyota continua sendo um exemplo de sucesso do Lean, com suas práticas contribuindo significativamente para sua posição como uma das principais fabricantes de automóveis.
Outras empresas, como a Hewlett-Packard, também adotaram os princípios Lean para otimizar suas operações e melhorar a eficiência de fabricação.
A filosofia Lean é reconhecida não apenas como uma simples coleção de ferramentas e técnicas, mas como uma filosofia de negócios abrangente que requer uma abordagem sistêmica e uma cultura que promova a melhoria contínua em todos os níveis organizacionais. Ela defende o empoderamento de todos os trabalhadores, permitindo que eles contribuam ativamente para aprimoramentos de processos e eliminação de desperdícios.
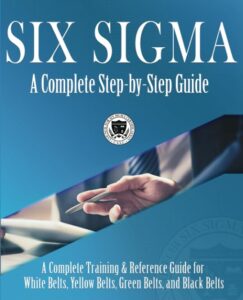
Os líderes Lean desempenham um papel crucial neste ambiente, atuando como treinadores e facilitadores das práticas de resolução de problemas e melhoria.
Os Cinco Princípios Lean
Valor: Todo processo deve começar reconhecendo o valor sob a perspectiva do cliente. O que realmente importa para o cliente? Este princípio instiga as empresas a focarem seus esforços no que é mais importante para o usuário final, garantindo que cada ação acrescente valor real.
Cadeia de Valor: Isso envolve mapear todos os passos envolvidos na entrega de um produto ou serviço – desde o início até a conclusão – e depois eliminar impiedosamente qualquer coisa que não agregue valor.
Fluxo contínuo: Ao garantir que o trabalho progrida de forma suave e previsível em cada etapa da produção, as empresas podem reduzir atrasos e gargalos, acelerando assim todo o processo.
Produção Puxada: Em vez de empurrar produtos para a próxima etapa de produção ou para o mercado, esse princípio defende que a produção seja ‘puxada’ com base na demanda do cliente, evitando assim a superprodução.
Perfeição: Finalmente, a busca pela perfeição é um processo iterativo onde a melhoria contínua é incentivada, sempre se esforçando para tornar o processo mais enxuto e eficiente.
Seis Sigma: A Evolução da Excelência
Six Sigma é uma metodologia que se concentra na melhoria de processos por meio da minimização de variabilidade e defeitos nos processos de negócios e manufatura. O conceito foi introduzido pelo engenheiro Bill Smith na Motorola em 1986 e posteriormente registrado pela empresa. Tornou-se mais amplamente conhecido e adotado após empresas como Honeywell e General Electric o implementarem, com o CEO da GE, Jack Welch, notavelmente integrando-o em sua estratégia de negócios em 1995.
As raízes do Six Sigma como um padrão de medição podem ser rastreadas até Carl Friedrich Gauss, que introduziu o conceito da curva normal. No entanto, como metodologia formalizada, o desenvolvimento do Six Sigma em termos de um sistema de gestão da qualidade surgiu na década de 1920 através do trabalho de Walter Shewhart, que demonstrou que um processo requer correção a três sigmas da média.
Esta metodologia é baseada na ideia de que um processo não deve produzir mais do que 3,4 defeitos por milhão de oportunidades, visando seis desvios padrão (sigma) entre a média do processo e o limite de especificação mais próximo.
A metodologia de Bill Smith foi ainda mais desenvolvida por Mikel Harry na Motorola, que formalizou o framework MAIC (Medir, Analisar, Melhorar, Controlar). Com o tempo, o Six Sigma evoluiu para incorporar a abordagem DMAIC (Definir, Medir, Analisar, Melhorar, Controlar), tornando-se um sistema completo para a melhoria de processos em diversas indústrias, não apenas na manufatura.
Muitas empresas Fortune 500 e outras organizações em todo o mundo adotaram o Six Sigma, percebendo economias significativas e melhorias nos processos como resultado. Essas empresas utilizaram com sucesso o Six Sigma para impulsionar a qualidade, eficiência e benefícios financeiros em suas operações.
O Bank of America, Caterpillar, Honeywell International, General Electric e 3M são exemplos notáveis de corporações que implementaram o Six Sigma e relataram melhorias e economias consideráveis.
O Six Sigma tem resistido ao teste do tempo devido à sua adaptabilidade e foi integrado a outras metodologias, como os princípios de manufatura enxuta, para formar o Lean Six Sigma. Essa abordagem combinada aproveita as forças de ambas as metodologias para melhorar ainda mais a eficiência e a qualidade dos processos.
Seis Sigma como uma ferramenta de domínio para a excelência
A adaptabilidade do Six Sigma em diferentes tamanhos de negócios e setores, desde pequenas empresas até companhias de transporte aéreo, destaca sua ampla aplicabilidade e eficácia. Essa metodologia tem sido implementada com sucesso por empresas ao redor do mundo, com o objetivo de reduzir defeitos, minimizar a variabilidade e melhorar a qualidade e eficiência geral.
A General Electric, sob a liderança de Jack Welch, se tornou um dos mais notáveis adotantes, integrando profundamente o Six Sigma em suas operações e cultura corporativa. Essa iniciativa não apenas resultou em economias financeiras significativas, mas também estabeleceu um precedente para outras empresas seguirem. Da mesma forma, as economias substanciais da Motorola atribuídas aos esforços do Six Sigma destacam o potencial da metodologia para impactar o resultado final (Six Sigma Online).
O Bank of America, uma instituição financeira líder, implementou o Lean Six Sigma para abordar questões de qualidade de processo, notadamente melhorando a satisfação do cliente ao reduzir erros e melhorar os tempos de processamento. A Caterpillar Inc., maior fabricante mundial de equipamentos de construção e mineração, introduziu o Six Sigma para analisar complicações e promover o crescimento, demonstrando a aplicabilidade da metodologia além dos tradicionais ambientes de manufatura.
A Honeywell International Inc. combinou dois eficazes Sistemas de Gestão da Qualidade através de uma fusão, integrando o Six Sigma para impulsionar melhorias em todos os seus processos, produtos e serviços, resultando em significativas melhorias de produtividade e ganhos financeiros. A Boeing Airlines, uma das maiores empresas aeroespaciais do mundo, aplicou métodos Six Sigma para resolver questões de fabricação, resultando em melhorias fundamentais em seus processos de produção.
Este conjunto de exemplos, desde a General Electric e Motorola até o Bank of America, Caterpillar, Honeywell e Boeing, demonstra a versatilidade e eficácia do Six Sigma em diferentes indústrias, incluindo finanças, manufatura, aeroespacial e tecnologia.
A metodologia com foco em reduzir desperdícios e defeitos, melhorar a qualidade e aumentar a eficiência é universalmente aplicável, tornando-se uma ferramenta valiosa para empresas de todos os tamanhos e setores. Para obter mais informações sobre a aplicação do Six Sigma em diversas indústrias.
Metodologia Seis Sigma: O tratamento livre de erros
A metodologia Seis Sigma, conhecida por seu rigoroso foco em reduzir erros e defeitos nos processos, utiliza uma medida estatística para avaliar a capacidade de um processo de realizar tarefas sem erros.
O próprio nome, Seis Sigma, faz referência ao objetivo de permitir apenas 3,4 defeitos por milhão de oportunidades, ajustando seis desvios padrão entre a média e o limite de especificação mais próximo em uma curva de distribuição do processo. Cada nível Sigma representa um passo mais próximo desse objetivo, com reduções significativas nas taxas de erro em cada nível.
Por exemplo, em um Sigma, um processo produziria um número substancial de defeitos, aproximadamente 690.000 por milhão de oportunidades, o que está longe de ser aceitável em qualquer indústria. Há medida que as empresas sobem nos níveis Sigma, o número de defeitos diminui drasticamente, demonstrando a eficácia da metodologia em melhorar a qualidade e a eficiência.
De maneira geral, a implementação do Six Sigma tem permitido às empresas reduzir drasticamente os erros, aprimorar a qualidade e garantir a satisfação do cliente, demonstrando a aplicabilidade universal e o valor da metodologia na busca pela excelência operacional.
Ferramentas Lean e Metas Seis Sigma
O pensamento enxuto é operacionalizado usando ferramentas como o Framework A3, que fornece uma abordagem estruturada para a resolução de problemas e melhoria contínua. Enquanto isso, os objetivos do Six Sigma se concentram em melhorar a satisfação do cliente e os processos de negócios. Ele tem como objetivo reduzir os tempos de ciclo, diminuir erros e padronizar as operações para garantir resultados de alta qualidade.
Ferramentas sinérgicas para Excelência de Processos
O diagrama SIPOC
O diagrama SIPOC (Fornecedores, Entradas, Processo, Saídas e Clientes), uma ferramenta utilizada na melhoria de processos, fornece uma visão geral dos processos de negócios, delineando os Fornecedores, Insumos, Processo, Saídas e Clientes envolvidos. Suas origens remontam aos programas de gestão de qualidade total do final da década de 1980 e tornou-se um pilar em metodologias como Six Sigma, manufatura enxuta e gestão de processos de negócios.
Organizações de diferentes setores têm utilizado diagramas SIPOC para obter uma compreensão mais clara de seus processos. Por exemplo, empresas de manufatura frequentemente os utilizam ao criar uma nova linha de produtos para garantir que todos os elementos do processo necessários sejam incluídos.
Hospitais podem empregá-los para identificar onde os pacientes experimentam atrasos desnecessários, e empresas de varejo podem reunir diferentes departamentos para otimizar os processos de entrega de produtos.
Quando se trata de criar um diagrama SIPOC, geralmente é feito desenhando uma tabela com cinco colunas e rotulando cada coluna com um elemento do SIPOC. Indivíduos com um conhecimento profundo do processo, então, preenchem cada coluna de acordo. Esse esforço colaborativo é essencial, pois reúne diferentes perspectivas e insights.
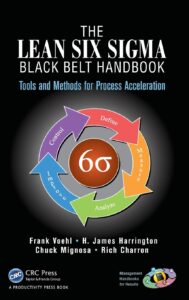
Existem várias ferramentas e softwares disponíveis para ajudar no desenvolvimento de diagramas SIPOC. Alguns dos conhecidos incluem softwares especializados de mapeamento de processos, como Visual Paradigm, Lucidchart e recursos online que oferecem modelos para a criação de SIPOC.
Essas ferramentas auxiliam equipes a mapear visualmente os processos e contribuir para os esforços de melhoria contínua em suas organizações.
O diagrama de Ishikawa
O diagrama de Ishikawa, também conhecido como diagrama de espinha de peixe ou diagrama de causa e efeito, foi desenvolvido por Kaoru Ishikawa na década de 1960. Ishikawa, um especialista japonês em controle de qualidade, introduziu esse diagrama para melhorar os processos de gestão da qualidade. Inicialmente utilizado nos estaleiros de Kawasaki, o diagrama tornou-se uma parte essencial das práticas modernas de gerenciamento.
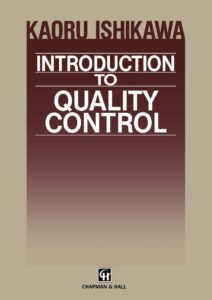
Uma empresa notável que utilizou o diagrama de Ishikawa é a Mazda Motors, que implementou a ferramenta no desenvolvimento do carro esportivo Miata (MX5).
O diagrama de Ishikawa é frequentemente utilizado no design de produtos e na prevenção de defeitos de qualidade para identificar potenciais fatores que causam um efeito geral, ajudando a identificar e categorizar fontes de variação.
As causas identificadas no diagrama são agrupadas em grandes categorias, como Mão de obra, Máquina, Material, Método e Medição, às vezes estendidas para incluir Missão, Gerenciamento e Manutenção, também conhecidas como os 8 Ms. Em indústrias de serviços, categorias alternativas como os 4 ou 5 Ss (Ambiente, Fornecedores, Sistemas, Habilidade e Segurança) são utilizadas.
A construção de um diagrama de Ishikawa envolve identificar e listar possíveis causas de um problema e categorizá-las. As equipes então analisam essas causas para identificar as causas raiz, muitas vezes usando técnicas como o método dos 5 Porquês. Uma vez que as causas raiz são determinadas, soluções podem ser desenvolvidas e implementadas para abordar essas causas e evitar que o problema se repita.
Ferramentas e softwares para criar diagramas de Ishikawa incluem diversas ferramentas especializadas de mapeamento de processos e gerenciamento de qualidade, que facilitam o desenho e o brainstorming das relações de causa e efeito visualmente. A estrutura do diagrama, com uma linha principal levando ao problema e ramos representando categorias de causas, permite que equipes identifiquem e resolvam sistematicamente as causas raiz dos problemas, melhorando os processos e resultados.
O diagrama de Ishikawa é considerado uma das sete ferramentas básicas de controle de qualidade e é amplamente utilizado em setores como manufatura, saúde e serviços, devido à sua eficácia na identificação de causas raiz e auxílio na melhoria de processos.
A estrutura FMEA
A estrutura FMEA (Análise de Modos e Efeitos de Falha) antecipa possíveis pontos de falha nos processos e ajuda a mitigá-los.
A Análise de Modos e Efeitos de Falhas (FMEA) é um método sistemático para identificar e abordar possíveis pontos de falha dentro de um sistema, produto ou processo. Ela surgiu nas décadas de 1940 e 1950, sendo amplamente utilizada nos setores militares e aeroespaciais para antecipar e prevenir possíveis falhas em sistemas críticos.
Inicialmente concebido para o exército dos Estados Unidos, os procedimentos para conduzir a FMEA foram descritos no documento de Procedimentos Militares MIL-P-1629, com a versão moderna da prática codificada em MIL-STD-1629A.
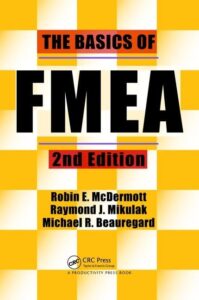
A metodologia FMEA evoluiu para incluir elementos quantitativos como o Número de Prioridade de Risco (NPR) na década de 1970, aprimorando sua precisão analítica. Com o crescimento de sistemas de gestão da qualidade como o Total Quality Management e Six Sigma nas décadas de 1980 e 1990, o FMEA se tornou um componente chave dos esforços de melhoria contínua dentro das organizações.
Ao longo dos anos, o FMEA foi adotado por várias indústrias, incluindo a automotiva, onde a Ford Motor Company o utilizou para informar sobre questões de segurança e regulamentação, e posteriormente o Automotive Industry Action Group publicou um padrão FMEA especificamente para a indústria automotiva. Hoje, indústrias que vão desde a saúde até o desenvolvimento de software utilizam o FMEA para mitigar riscos e aprimorar a qualidade e segurança.
O FMEA é suportado por várias ferramentas digitais que fornecem cálculos de risco automatizados e plataformas colaborativas, permitindo uma análise e relatórios eficientes. Essas ferramentas e a integração do FMEA com outras técnicas analíticas, como a Análise de Árvore de Falhas (FTA), mantiveram a metodologia relevante e adaptável às necessidades em constante mudança das indústrias modernas, focadas em confiabilidade, segurança e excelência.
A metodologia 5S
A metodologia 5S (Classificar, Organizar, Limpar, Padronizar, Sustentar) oferece uma abordagem sistemática para organizar o local de trabalho que apoia a eficiência e a eficácia.
A metodologia 5S é uma abordagem sistemática para a organização e padronização no local de trabalho, originária do Japão e um componente fundamental do sistema de produção enxuta. Desenvolvida no Japão, foi identificada como uma das técnicas que permitiram a fabricação just-in-time, especialmente na Toyota na década de 1950.
A bem-sucedida integração dos princípios 5S da Toyota em seu sistema de produção contribuiu para sua ascensão como uma das principais fabricantes de automóveis e ajudou a disseminar a metodologia em indústrias ao redor do mundo.
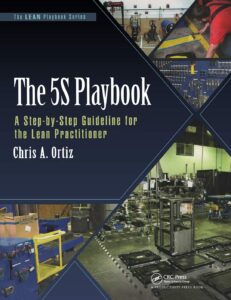
Os princípios fundamentais do 5S, conhecidos em japonês como seiri (separar), seiton (organizar), seisō (limpar), seiketsu (padronizar) e shitsuke (manter), orientam as organizações a manter um espaço de trabalho limpo, organizado e sem desordem. Esses passos têm como objetivo aumentar a eficiência, a segurança e a fluidez geral do fluxo de trabalho.
Organizações fora da indústria manufatureira, incluindo saúde, educação e varejo, também adotaram o 5S, descobrindo que seus princípios universalmente apoiam a eficiência operacional e uma cultura de melhoria contínua.
Para implementar o 5S, as empresas frequentemente utilizam auditorias e ferramentas de gerenciamento visual para manter e melhorar o sistema 5S estabelecido. Essas auditorias são fundamentais para garantir o sucesso da metodologia, pois ajudam a confirmar o entendimento e a implementação adequados dos princípios do 5S. A introdução da metodologia 6S, que incorpora a segurança como um princípio adicional, destaca a adaptabilidade da metodologia e o compromisso em criar ambientes de trabalho seguros.
Quanto às ferramentas, várias soluções de software suportam a implementação e auditoria da metodologia 5S. Elas oferecem recursos para rastrear o progresso, facilitar a comunicação e garantir a conformidade com os padrões 5S. A digitalização das práticas 5S por meio dessas ferramentas ainda otimiza o processo e o integra às operações modernas de negócios.
O uso do 5S, sua implementação estruturada e auditoria contínua podem levar a uma redução significativa de desperdício, melhoria na produtividade e aumento da segurança no local de trabalho. Ele permite a organização dos espaços físicos, bem como a otimização dos fluxos de trabalho em vários ambientes operacionais, incluindo tanto ambientes de produtos quanto de serviços (SafetyCulture).
Lean Six Sigma na Gestão de Processos de Negócios (BPM)
No reino do BPM, todas as abordagens de gestão convergem, e o Lean Six Sigma se destaca como um dos principais impulsionadores da excelência de processos. Profissionais de BPM utilizam o Lean Six Sigma para otimizar fluxos de trabalho, eliminar desperdícios e garantir qualidade, elementos essenciais no cenário competitivo atual.
O Valor para Profissionais
Para profissionais versados em Lean Six Sigma dentro do BPM, o valor é claro. Eles possuem a capacidade não apenas de aprimorar o desempenho operacional, mas também de gerar economias financeiras significativas e melhorias na satisfação do cliente. Essas habilidades estão em alta demanda, já que as organizações buscam otimizar seus processos e garantir a qualidade.
Pronto para impulsionar sua carreira e promover mudanças significativas em sua organização? Nosso curso BPM Fast Mode irá equipá-lo com as ferramentas e conhecimentos necessários para aplicar os princípios do Lean Six Sigma de forma efetiva.
Junte-se a nós no BPM Fast Mode e comece sua jornada para se tornar um campeão da excelência de processos. Seu caminho para dominar o Lean Six Sigma e transformar os processos de negócios começa aqui. Inscreva-se agora e seja o profissional que não apenas entende o processo, mas o melhora continuamente.