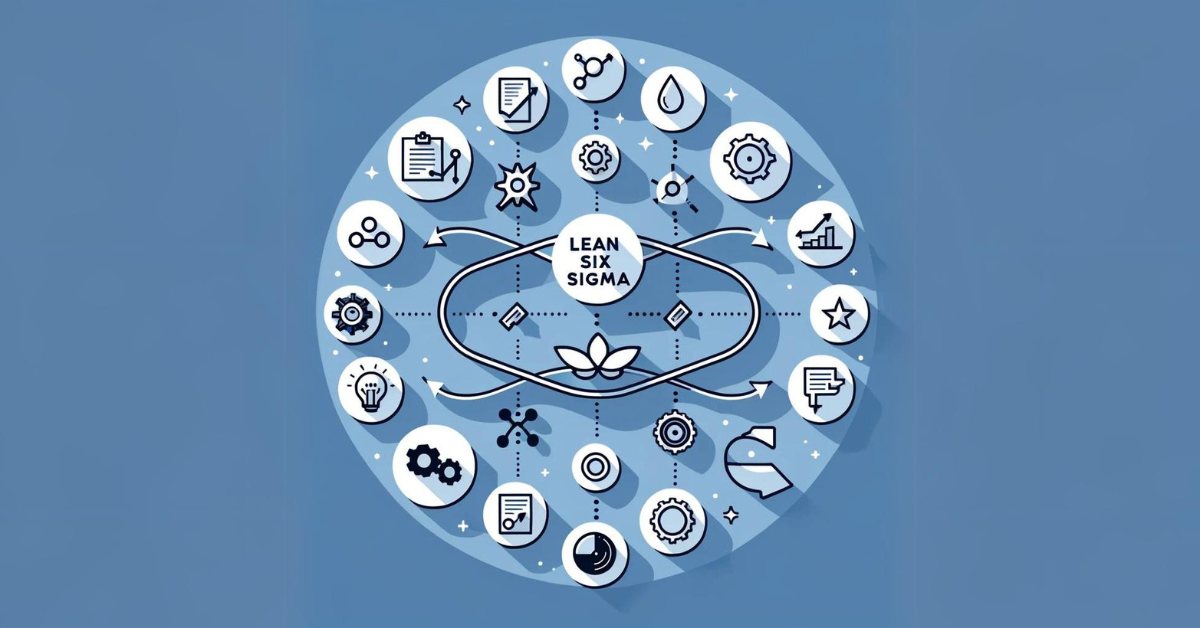
Lean Six Sigma: Synergizing Efficiency and Quality
Lean Six Sigma represents a merger of two powerful process improvement methodologies: Lean, which focuses on waste reduction and efficiency, and Six Sigma, which targets quality and precision by eliminating defects. When combined, they form a comprehensive approach to operational excellence.
Maximizing Efficiency: The Impact of Lean Philosophy on Modern Business Practices
Lean philosophy is a systematic approach to identifying and eliminating waste through continuous improvement, rooted in the Toyota Production System (TPS) from the mid-20th century. The concept is grounded in defining value from the customer’s perspective and ensuring that value creation occurs with minimal waste.
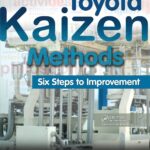
This philosophy originated with the efficient manufacturing operations of Toyota, which established principles aimed at eliminating waste and streamlining production processes.
Henry Ford is often cited as an early contributor to the Lean mindset with his flow production system at Highland Park, which emphasized standard work and moving conveyance to maximize efficiency. However, it was the Toyota engineers, most notably Taiichi Ohno and Shigeo Shingo, who developed these ideas into the more comprehensive TPS in the post-World War II era.
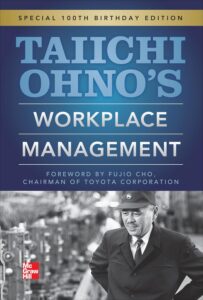
Toyota’s system was built on the principles of just-in-time inventory management and automated quality control, aiming to achieve a harmonious flow in the production process while embracing a philosophy of continuous improvement.
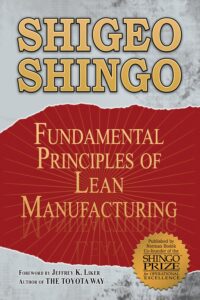
The term ‘Lean’ itself was coined much later, in 1988, by John Krafcik, and it was subsequently defined and popularized in the book ‘The Machine That Changed the World’ by James P. Womack, Daniel T. Jones, and Daniel Roos. They outlined the key principles of Lean as value, value stream, flow, pull, and perfection, each playing a crucial role in reducing waste and improving productivity.
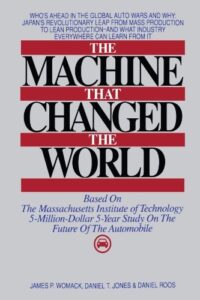
Today, Lean philosophy is applied not just in manufacturing but also in various sectors such as healthcare, software development, education, and more.
Companies across these industries employ Lean strategies to increase efficiency, reduce waste, and enhance overall productivity. For instance, Toyota continues to be a leading example of Lean’s success, with its practices contributing significantly to its position as a top automobile manufacturer.
Other companies, like Hewlett-Packard, have also adopted Lean principles to streamline their operations and improve manufacturing efficiency.
Lean philosophy is recognized not as a mere collection of tools and techniques but as a comprehensive business philosophy that requires a systemic approach and a culture that fosters continuous improvement at all organizational levels. It advocates for the empowerment of all workers, enabling them to contribute to process enhancements and waste elimination actively.
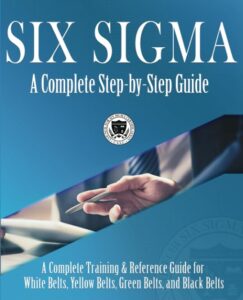
Lean leaders play a crucial role in this environment, acting as coaches and facilitators of problem-solving and improvement practices.
The Five Lean Principles
Value: Every process should begin by recognizing value from the customer’s perspective. What does the customer truly care about? This principle urges businesses to focus efforts on what matters most to the end user, ensuring that every action adds real value.
Value Stream: This involves mapping out all the steps involved in delivering a product or service – from inception to completion – and then ruthlessly eliminating anything that doesn’t add value.
Continuous Flow: By ensuring that work progresses smoothly and predictably through each stage of production, businesses can reduce delays and bottlenecks, thus speeding up the entire process.
Pulled Production: Instead of pushing products onto the next stage of production or into the market, this principle advocates for production to be ‘pulled’ based on customer demand, thus preventing overproduction.
Perfection: Finally, the pursuit of perfection is an iterative process where continuous improvement is encouraged, always striving to make the process leaner and more efficient.
Six Sigma: The Evolution of Excellence
Six Sigma is a methodology that focuses on process improvement by minimizing variability and defects in business and manufacturing processes. The concept was introduced by engineer Bill Smith at Motorola in 1986 and later trademarked by the company. It became more widely known and adopted after companies like Honeywell and General Electric implemented it, with GE’s CEO Jack Welch notably integrating it into his business strategy in 1995.
The roots of Six Sigma as a measurement standard can be traced back to Carl Friedrich Gauss who introduced the concept of the normal curve. However, as a formalized methodology, Six Sigma’s development in terms of a quality management system came about in the 1920s through the work of Walter Shewhart, who demonstrated that a process requires correction at three sigma from the mean.
This methodology is based on the idea that a process should not produce more than 3.4 defects per million opportunities, aiming for six standard deviations (sigma) between the process mean and the nearest specification limit.
Bill Smith’s methodology was further developed by Mikel Harry at Motorola, who formalized the MAIC (Measure, Analyze, Improve, Control) framework. Over time, Six Sigma evolved to incorporate the DMAIC (Define, Measure, Analyze, Improve, Control) approach, becoming a full-fledged system for process improvement across industries, not just manufacturing.
Many Fortune 500 companies and other organizations worldwide have adopted Six Sigma, realizing significant savings and process improvements as a result. These companies have successfully used Six Sigma to drive quality, efficiency, and financial benefits across their operations. Bank of America, Caterpillar, Honeywell International, General Electric, and 3M are notable examples of corporations that have implemented Six Sigma and reported considerable improvements and savings.
Six Sigma has stood the test of time due to its adaptability and has been integrated with other methodologies, such as Lean manufacturing principles, to form Lean Six Sigma. This combined approach leverages the strengths of both methodologies to further enhance process efficiency and quality.
Six Sigma as a mastering tool to excellence
Six Sigma’s adaptability across various business sizes and sectors, from small businesses to air transportation companies, underscores its wide applicability and effectiveness. This methodology has been implemented successfully by companies around the globe, aiming to reduce defects, minimize variability, and improve overall quality and efficiency.
General Electric, under the leadership of Jack Welch, became one of the most notable adopters, integrating Six Sigma deeply into its operations and corporate culture. This move not only resulted in significant financial savings but also set a precedent for other companies to follow. Similarly, Motorola’s substantial savings attributed to Six Sigma efforts highlight the methodology’s potential for impacting the bottom line (Six Sigma Online).
Bank of America, a leading financial institution, implemented Lean Six Sigma to address issues in process quality, notably improving customer satisfaction by reducing errors and improving processing times. Caterpillar Inc., the world’s largest manufacturer of construction and mining equipment, introduced Six Sigma to analyze complications and foster growth, demonstrating the methodology’s applicability beyond traditional manufacturing settings.
Honeywell International Inc. combined two effective Quality Management Systems through a merger, integrating Six Sigma to drive improvements across all its processes, products, and services, resulting in significant productivity improvements and financial gains. Boeing Airlines, one of the world’s largest aerospace companies, applied Six Sigma methods to address manufacturing issues, leading to fundamental improvements in their production processes.
This array of examples, from General Electric and Motorola to Bank of America, Caterpillar, Honeywell, and Boeing, showcases Six Sigma’s versatility and effectiveness across different industries, including finance, manufacturing, aerospace, and technology.
The methodology’s focus on reducing waste and defects, improving quality, and increasing efficiency is universally applicable, making it a valuable tool for businesses of all sizes and sectors.
Six Sigma Methodology: The error free treatment
Six Sigma methodology, known for its rigorous focus on reducing errors and defects in processes, uses a statistical measure to gauge the capability of a process to perform error-free.
The name itself, Six Sigma, references the goal of allowing only 3.4 defects per million opportunities by fitting six standard deviations between the mean and the nearest specification limit in a process distribution curve. Each Sigma level represents a step closer to this goal, with significant reductions in error rates at each level.
For example, at one Sigma, a process would produce a substantial number of defects, approximately 690,000 per million opportunities, which is far from acceptable in any industry. As companies climb the Sigma levels, the number of defects drastically decreases, demonstrating the methodology’s efficacy in improving quality and efficiency.
Across the board, the implementation of Six Sigma has allowed companies to reduce errors dramatically, enhance quality, and ensure customer satisfaction, demonstrating the methodology’s universal applicability and value in achieving operational excellence.
Lean Tools and Six Sigma Goals
Lean thinking is operationalized using tools like the A3 Framework, which provides a structured approach to problem-solving and continuous improvement. Meanwhile, the goals of Six Sigma center on enhancing customer satisfaction and business processes. It aims to slash cycle times, reduce errors, and standardize operations to ensure high-quality outcomes.
Synergistic Tools for Process Excellence
SIPOC diagram
The SIPOC diagram (Suppliers, Inputs, Process, Outputs, and Customers) provides a high-level view of the process, helping in understanding the flow and identifying potential areas for improvement.
The SIPOC diagram, a tool used in process improvement, provides a high-level view of business processes, outlining the Suppliers, Inputs, Process, Outputs, and Customers involved. Its origins date back to the total quality management programs of the late 1980s and it has become a mainstay in methodologies such as Six Sigma, lean manufacturing, and business process management.
Organizations across various industries have utilized SIPOC diagrams to gain a clearer understanding of their processes. For instance, manufacturing companies often use them when creating a new product line to ensure all necessary process elements are included. Hospitals might employ them to identify where patients experience unnecessary delays, and retail companies can bring together different departments to optimize product delivery processes.
When it comes to creating a SIPOC diagram, it’s usually done by drawing a table with five columns and labeling each column with one element of SIPOC. Individuals with a thorough knowledge of the process then fill out each column accordingly. This collaborative effort is essential as it brings together different perspectives and insights.
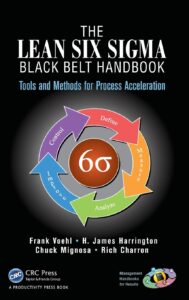
There are various tools and software available to help with the development of SIPOC diagrams. Some of the known tools include specialized process mapping software like Visual Paradigm, Lucidchart, and online resources that offer templates for SIPOC creation. These tools assist teams in visually mapping out the processes and contributing to continuous improvement efforts within their organizations.
Ishikawa diagram
The Ishikawa diagram, or fishbone diagram, aids in root cause analysis, allowing teams to trace back sources of defects.
The Ishikawa diagram, also known as the fishbone diagram or cause-and-effect diagram, was developed by Kaoru Ishikawa in the 1960s. Ishikawa, a Japanese quality control expert, introduced this diagram to improve quality management processes. Initially used in the Kawasaki shipyards, the diagram became an essential part of modern management practices.
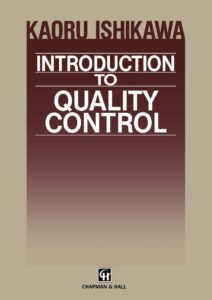
One notable company that utilized the Ishikawa diagram is Mazda Motors, which implemented the tool in the development of the Miata (MX5) sports car.
The Ishikawa diagram is often used in product design and quality defect prevention to identify potential factors causing an overall effect, helping to identify and categorize sources of variation.
The causes identified in the diagram are grouped into major categories, such as Manpower, Machine, Material, Method, and Measurement, sometimes extended to include Mission, Management, and Maintenance, also known as the 8 Ms. In service industries, alternative categories like the 4 or 5 Ss (Surroundings, Suppliers, Systems, Skill, and Safety) are used.
The construction of an Ishikawa diagram involves identifying and listing potential causes of a problem and categorizing them. Teams then analyze these causes to identify root causes, often using techniques like the 5 Whys method. Once root causes are determined, solutions can be developed and implemented to address these causes and prevent the problem from recurring.
Tools and software to create Ishikawa diagrams include various specialized process mapping and quality management tools, which facilitate drawing and brainstorming the cause-and-effect relationships visually. The diagram’s structure, with a main line leading to the problem and branches representing categories of causes, allows teams to systematically identify and tackle the root causes of problems, ultimately improving processes and outcomes.
The Ishikawa diagram is considered one of the seven basic tools of quality control and is widely used across industries like manufacturing, healthcare, and services due to its effectiveness in identifying root causes and aiding in process improvement.
FMEA framework
The FMEA framework (Failure Modes and Effects Analysis) anticipates potential points of failure in processes and helps in mitigating them.
The Failure Modes and Effects Analysis (FMEA) is a systematic method for identifying and addressing potential failure points within a system, product, or process. It originated in the 1940s and 1950s, finding significant use within the military and aerospace sectors to anticipate and prevent potential failures in critical systems.
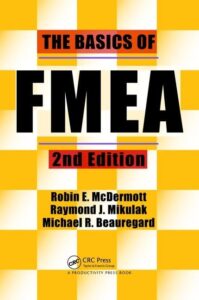
Initially devised for the U.S. military, procedures for conducting FMEA were described in the Military Procedures document MIL-P-1629, with the modern version of the practice codified in MIL-STD-1629A.
FMEA methodology evolved to include quantitative elements such as the Risk Priority Number (RPN) in the 1970s, enhancing its analytical precision. As quality management systems like Total Quality Management and Six Sigma grew in the 1980s and 1990s, FMEA became a key component of continuous improvement efforts within organizations.
Over the years, FMEA has been adopted by various industries, including automotive, where Ford Motor Company used it to inform safety and regulatory considerations, and later the Automotive Industry Action Group published an FMEA standard specifically for the automotive industry. Today, industries ranging from healthcare to software development use FMEA to mitigate risks and enhance quality and safety.
FMEA is supported by various digital tools that provide automated risk calculations and collaborative platforms, allowing for efficient analysis and reporting. These tools and the integration of FMEA with other analytical techniques such as Fault Tree Analysis (FTA) have kept the methodology relevant and adaptable to the changing needs of modern industries focused on reliability, safety, and excellence.
See Visure Solutions that offers insights into the evolution of this critical risk management tool.
5S methodology
The 5S methodology (Sort, Set in order, Shine, Standardize, Sustain) offers a systematic approach to organizing the workplace that supports efficiency and effectiveness.
The 5S methodology is a systematic approach for workplace organization and standardization, originating from Japan and a fundamental component of the lean manufacturing system. Developed in Japan, it was identified as one of the techniques enabling just-in-time manufacturing, particularly at Toyota in the 1950s.
Toyota’s successful integration of 5S principles into its production system contributed to its rise as a leading automobile manufacturer and helped proliferate the methodology across industries worldwide.
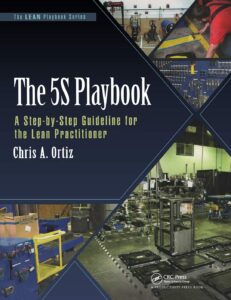
The core principles of 5S, known in Japanese as seiri (sort), seiton (set in order), seisō (shine), seiketsu (standardize), and shitsuke (sustain), guide organizations to maintain a clean, uncluttered, and well-organized workspace. These steps aim to increase efficiency, safety, and overall workflow smoothness.
Organizations outside of manufacturing, including healthcare, education, and retail, have also adopted 5S, finding that its principles universally support operational efficiency and a culture of continuous improvement.
For implementing 5S, companies often utilize audits and visual management tools to maintain and improve the established 5S system. These audits are critical to ensuring the methodology’s success, as they help confirm the proper understanding and implementation of the 5S principles. The introduction of the 6S methodology, which incorporates safety as an additional principle, underscores the methodology’s adaptability and commitment to creating secure work environments.
As for tools, several software solutions support the implementation and auditing of the 5S methodology. They offer features for tracking progress, facilitating communication, and ensuring compliance with 5S standards. The digitalization of 5S practices through these tools further streamlines the process and integrates it into modern business operations.
The use of 5S, its structured implementation, and continuous auditing can lead to significant waste reduction, improved productivity, and enhanced workplace safety. It allows for the organization of physical spaces as well as optimization of workflows in various operational settings, including both product and service-oriented environments (SafetyCulture).
Lean Six Sigma in Business Process Management (BPM)
In the realm of BPM, all management approaches converge, and Lean Six Sigma stands out as a prime driver of process excellence. BPM professionals use Lean Six Sigma to streamline workflows, eliminate waste, and ensure quality, which are essential in today’s competitive landscape.
The Value for Professionals
For professionals versed in Lean Six Sigma within BPM, the value is clear. They possess the capability not only to enhance operational performance but also to drive significant financial savings and customer satisfaction improvements. These skills are in high demand as organizations seek to optimize their processes and ensure quality.
Ready to enhance your career and drive meaningful change in your organization? Our BPM Fast Mode course will equip you with the tools and knowledge to apply Lean Six Sigma principles effectively.
Join us at BPM Fast Mode, and begin your journey to becoming a champion of process excellence. Your path to mastering Lean Six Sigma and transforming business processes starts here. Sign up now and be the professional who not only understands the process but improves it continuously.