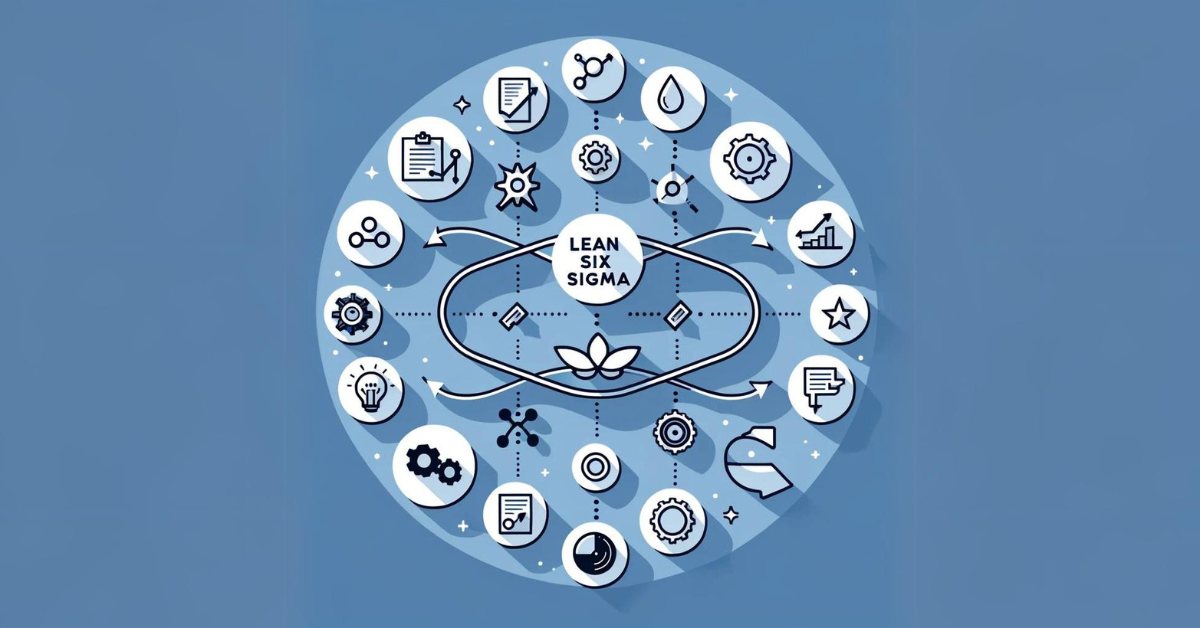
Lean Six Sigma: Sinergizando Eficiencia y Calidad
Lean Six Sigma representa una fusión de dos poderosas metodologías de mejora de procesos: Lean, que se enfoca en la reducción de desperdicios y la eficiencia, y Six Sigma, que apunta a la calidad y precisión al eliminar defectos. Cuando se combinan, forman un enfoque integral para la excelencia operativa.
Maximizando la eficiencia: El impacto de la filosofía Lean en las prácticas empresariales modernas
La filosofía Lean es un enfoque sistemático para identificar y eliminar el desperdicio a través de la mejora continua, basado en el Sistema de Producción de Toyota (TPS) de mediados del siglo XX. El concepto se basa en definir el valor desde la perspectiva del cliente y garantizar que la creación de valor se produzca con un mínimo de desperdicio. Esta filosofía se originó en las operaciones de fabricación eficientes de Toyota, que estableció principios orientados a eliminar el desperdicio.
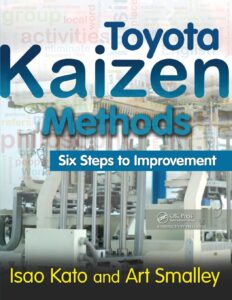
Esta filosofía se originó con las operaciones eficientes de fabricación de Toyota, que estableció principios orientados a eliminar el desperdicio y optimizar los procesos de producción.
Henry Ford es frecuentemente citado como un contribuyente temprano al pensamiento Lean con su sistema de producción en flujo en Highland Park, que enfatizaba el trabajo estándar y el transporte en movimiento para maximizar la eficiencia. Sin embargo, fueron los ingenieros de Toyota, especialmente Taiichi Ohno y Shigeo Shingo, quienes desarrollaron estas ideas en el más completo TPS en la era de la posguerra.
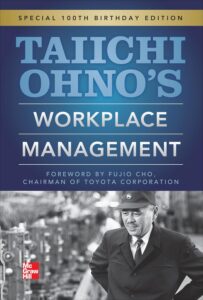
El sistema de Toyota fue construido sobre los principios de gestión de inventario justo a tiempo y control de calidad automatizado, con el objetivo de lograr un flujo armonioso en el proceso de producción mientras se abraza una filosofía de mejora continua.
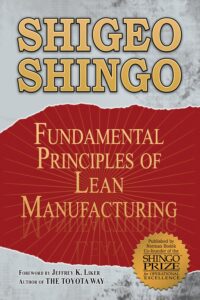
El término ‘Lean’ en sí fue acuñado mucho después, en 1988, por John Krafcik, y posteriormente fue definido y popularizado en el libro ‘The Machine That Changed the World’ por James P. Womack, Daniel T. Jones y Daniel Roos. Ellos delinearon los principios clave de Lean como valor, flujo, tirón y perfección, cada uno desempeñando un papel crucial en la reducción de desperdicios y en la mejora de la productividad.
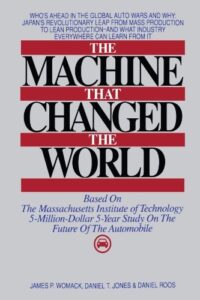
Hoy en día, la filosofía Lean se aplica no solo en la fabricación, sino también en varios sectores como la atención médica, el desarrollo de software, la educación y más. Las empresas en estas industrias emplean estrategias Lean para aumentar la eficiencia, reducir el desperdicio y mejorar la productividad en general. Por ejemplo, Toyota sigue siendo un ejemplo líder del éxito de Lean, con sus prácticas contribuyendo significativamente a su posición como uno de los principales fabricantes de automóviles. Otras compañías, como Hewlett-Packard, también han adoptado los principios de Lean para agilizar sus operaciones y mejorar la eficiencia en la fabricación.
La filosofía Lean es reconocida no solo como una simple colección de herramientas y técnicas, sino como una filosofía empresarial integral que requiere un enfoque sistémico y una cultura que fomente la mejora continua en todos los niveles organizativos. Aboga por el empoderamiento de todos los trabajadores, permitiéndoles contribuir activamente a la mejora de procesos y la eliminación de desperdicios.
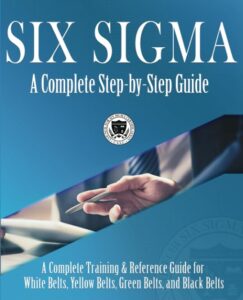
Los líderes Lean desempeñan un papel crucial en este entorno, actuando como entrenadores y facilitadores de prácticas de resolución de problemas y mejora.
Los Cinco Principios del Lean
Valor: Cada proceso debe comenzar reconociendo el valor desde la perspectiva del cliente. ¿Qué es lo que realmente le importa al cliente? Este principio insta a las empresas a enfocar sus esfuerzos en lo que más importa al usuario final, asegurando que cada acción agregue un valor real.
Cadena de valor: Esto implica trazar todos los pasos involucrados en la entrega de un producto o servicio – desde su inicio hasta su finalización – y luego eliminar sin piedad cualquier cosa que no agregue valor.
Flujo continuo: Al asegurarse de que el trabajo avance de manera fluida y predecible en cada etapa de producción, las empresas pueden reducir retrasos y cuellos de botella, acelerando así todo el proceso.
Producción por Demanda: En lugar de empujar los productos hacia la siguiente etapa de producción o hacia el mercado, este principio aboga por una producción «por demanda» basada en las necesidades del cliente, evitando así la sobreproducción.
Perfección: Finalmente, la búsqueda de la perfección es un proceso iterativo donde se fomenta la mejora continua, siempre esforzándose por hacer el proceso más ágil y eficiente.
Seis Sigma: La Evolución de la Excelencia
Seis Sigma es una metodología que se enfoca en la mejora de procesos al minimizar la variabilidad y los defectos en los procesos comerciales y de fabricación. El concepto fue introducido por el ingeniero Bill Smith en Motorola en 1986 y posteriormente fue registrado por la compañía. Se hizo más conocido y adoptado después de que empresas como Honeywell y General Electric lo implementaran, con el CEO de GE, Jack Welch, integrándolo notablemente en su estrategia empresarial en 1995.
Las raíces de Six Sigma como estándar de medición se remontan a Carl Friedrich Gauss, quien introdujo el concepto de la curva normal. Sin embargo, como metodología formalizada, el desarrollo de Six Sigma como sistema de gestión de calidad surgió en la década de 1920 a través del trabajo de Walter Shewhart, quien demostró que un proceso requiere corrección a tres sigma de la media.
Esta metodología se basa en la idea de que un proceso no debe producir más de 3.4 defectos por millón de oportunidades, apuntando a seis desviaciones estándar (sigma) entre la media del proceso y el límite de especificación más cercano.
La metodología de Bill Smith fue desarrollada aún más por Mikel Harry en Motorola, quien formalizó el marco MAIC (Medir, Analizar, Mejorar, Controlar). Con el tiempo, Seis Sigma evolucionó para incorporar el enfoque DMAIC (Definir, Medir, Analizar, Mejorar, Controlar), convirtiéndose en un sistema completo para la mejora de procesos en todas las industrias, no solo en la manufactura.
Muchas empresas Fortune 500 y otras organizaciones en todo el mundo han adoptado Seis Sigma, logrando ahorros significativos y mejoras en sus procesos como resultado. Estas empresas han utilizado con éxito Seis Sigma para impulsar la calidad, eficiencia y beneficios financieros en todas sus operaciones.
Bank of America, Caterpillar, Honeywell International, General Electric y 3M son ejemplos destacados de corporaciones que han implementado Seis Sigma y han reportado mejoras y ahorros considerable.
Seis Sigma ha resistido la prueba del tiempo debido a su adaptabilidad y se ha integrado con otras metodologías, como los principios de fabricación Lean, para formar Lean Six Sigma. Este enfoque combinado aprovecha las fortalezas de ambas metodologías para mejorar aún más la eficiencia y la calidad del proceso.
Seis Sigma como una herramienta de dominio para la excelencia
La adaptabilidad de Six Sigma en diferentes tamaños y sectores empresariales, desde pequeñas empresas hasta compañías de transporte aéreo, subraya su amplia aplicabilidad y efectividad. Esta metodología ha sido implementada exitosamente por empresas en todo el mundo, con el objetivo de reducir defectos, minimizar la variabilidad y mejorar la calidad y eficiencia en general.
General Electric, bajo el liderazgo de Jack Welch, se convirtió en uno de los adoptantes más notables, integrando Six Sigma profundamente en sus operaciones y cultura corporativa. Este movimiento no solo resultó en importantes ahorros financieros, sino que también estableció un precedente para que otras empresas lo siguieran. De manera similar, los ahorros sustanciales de Motorola atribuidos a los esfuerzos de Six Sigma destacan el potencial de la metodología para impactar en la línea de fondo (Six Sigma Online).
Banco de América, una institución financiera líder, implementó Lean Six Sigma para abordar problemas en la calidad del proceso, notablemente mejorando la satisfacción del cliente al reducir errores y mejorar los tiempos de procesamiento. Caterpillar Inc., el mayor fabricante mundial de equipos de construcción y minería, introdujo Six Sigma para analizar complicaciones y fomentar el crecimiento, demostrando la aplicabilidad de la metodología más allá de los entornos de fabricación tradicionales.
Honeywell International Inc. combinó dos sistemas efectivos de Gestión de Calidad a través de una fusión, integrando Six Sigma para impulsar mejoras en todos sus procesos, productos y servicios, lo que resultó en importantes mejoras en la productividad y ganancias financieras. Boeing Airlines, una de las compañías aeroespaciales más grandes del mundo, aplicó métodos Six Sigma para abordar problemas de fabricación, lo que llevó a mejoras fundamentales en sus procesos de producción.
Esta variedad de ejemplos, desde General Electric y Motorola hasta Bank of America, Caterpillar, Honeywell y Boeing, demuestra la versatilidad y eficacia de Six Sigma en diferentes industrias, incluyendo finanzas, manufactura, aeroespacial y tecnología.
La metodología enfocada en reducir el desperdicio y defectos, mejorar la calidad y aumentar la eficiencia es universalmente aplicable, lo que la convierte en una herramienta valiosa para empresas de todos los tamaños y sectores. Para obtener más información sobre la aplicación de Six Sigma en diferentes industias.
Metodología Seis Sigma: El tratamiento sin errores
La metodología Seis Sigma, conocida por su enfoque riguroso en la reducción de errores y defectos en los procesos, utiliza una medida estadística para evaluar la capacidad de un proceso para realizar sin errores.
El nombre en sí, Seis Sigma, hace referencia al objetivo de permitir solo 3.4 defectos por millón de oportunidades al ajustar seis desviaciones estándar entre la media y el límite de especificación más cercano en una curva de distribución del proceso. Cada nivel Sigma representa un paso más cerca de este objetivo, con reducciones significativas en las tasas de error en cada nivel.
Por ejemplo, en un Sigma, un proceso produciría una cantidad considerable de defectos, aproximadamente 690,000 por cada millón de oportunidades, lo cual está muy lejos de ser aceptable en cualquier industria. A medida que las empresas suben de nivel en Sigma, la cantidad de defectos disminuye drásticamente, demostrando la eficacia de la metodología en mejorar la calidad y eficiencia.
En general, la implementación de Six Sigma ha permitido a las empresas reducir drásticamente los errores, mejorar la calidad y garantizar la satisfacción del cliente, demostrando la aplicabilidad universal y el valor de la metodología para lograr la excelencia operativa.
Herramientas Lean y Objetivos de Seis Sigma
El pensamiento Lean se opera utilizando herramientas como el Marco A3, que proporciona un enfoque estructurado para resolver problemas y mejorar continuamente. Mientras tanto, los objetivos de Six Sigma se centran en mejorar la satisfacción del cliente y los procesos empresariales. Su objetivo es reducir los tiempos de ciclo, disminuir los errores y estandarizar las operaciones para garantizar resultados de alta calidad.
Herramientas sinérgicas para la excelencia en procesos
El diagrama SIPOC
El diagrama SIPOC (Proveedores, Insumos, Proceso, Salidas y Clientes), una herramienta utilizada en la mejora de procesos, proporciona una visión de alto nivel de los procesos empresariales, delineando a los Proveedores, Insumos, Proceso, Productos y Clientes involucrados. Sus orígenes se remontan a los programas de gestión de calidad total de finales de los años 80 y se ha convertido en un elemento fundamental en metodologías como Six Sigma, fabricación esbelta y gestión de procesos empresariales.
Las organizaciones en diversas industrias han utilizado los diagramas SIPOC para obtener una comprensión más clara de sus procesos. Por ejemplo, las empresas de fabricación a menudo los utilizan al crear una nueva línea de productos para asegurarse de que se incluyan todos los elementos necesarios del proceso. Los hospitales pueden emplearlos para identificar dónde los pacientes experimentan retrasos innecesarios, y las empresas minoristas pueden reunir diferentes departamentos para optimizar los procesos de entrega de productos.
Cuando se trata de crear un diagrama SIPOC, generalmente se hace dibujando una tabla con cinco columnas y etiquetando cada columna con un elemento de SIPOC. Las personas con un conocimiento profundo del proceso luego completan cada columna en consecuencia. Este esfuerzo colaborativo es esencial ya que reúne diferentes perspectivas y conocimientos.
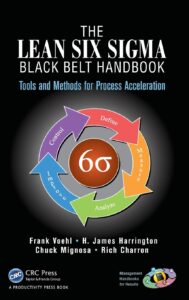
Hay varias herramientas y software disponibles para ayudar con el desarrollo de diagramas SIPOC. Algunas de las herramientas conocidas incluyen software especializado de mapeo de procesos como Visual Paradigm, Lucidchart y recursos en línea que ofrecen plantillas para la creación de SIPOC. Estas herramientas ayudan a los equipos a mapear visualmente los procesos y contribuyen a los esfuerzos de mejora continua dentro de sus organizaciones.
El diagrama de Ishikawa
El diagrama de Ishikawa, también conocido como diagrama de espina de pescado o diagrama de causa y efecto, fue desarrollado por Kaoru Ishikawa en la década de 1960. Ishikawa, un experto japonés en control de calidad, introdujo este diagrama para mejorar los procesos de gestión de calidad. Inicialmente utilizado en los astilleros de Kawasaki, el diagrama se convirtió en una parte esencial de las prácticas modernas de gestión.
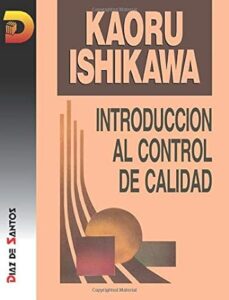
Una empresa notable que utilizó el diagrama de Ishikawa es Mazda Motors, que implementó la herramienta en el desarrollo del auto deportivo Miata (MX5).
El diagrama de Ishikawa se utiliza frecuentemente en el diseño de productos y la prevención de defectos de calidad para identificar posibles factores que causan un efecto general, ayudando a identificar y categorizar fuentes de variación.
Las causas identificadas en el diagrama se agrupan en categorías principales, como Mano de obra, Máquina, Material, Método y Medición, a veces extendidas para incluir Misión, Gestión y Mantenimiento, también conocidas como las 8 M. En industrias de servicios, se utilizan categorías alternativas como las 4 o 5 S (Entorno, Proveedores, Sistemas, Habilidad y Seguridad).
La construcción de un diagrama de Ishikawa implica identificar y listar posibles causas de un problema y categorizarlas. Los equipos luego analizan estas causas para identificar las causas raíz, a menudo utilizando técnicas como el método de las 5 Porqués. Una vez determinadas las causas raíz, se pueden desarrollar e implementar soluciones para abordar estas causas y evitar que el problema vuelva a ocurrir.
Las herramientas y software para crear diagramas de Ishikawa incluyen diversas herramientas especializadas de mapeo de procesos y gestión de calidad, que facilitan el dibujo y la lluvia de ideas de las relaciones causa-efecto de manera visual. La estructura del diagrama, con una línea principal que lleva al problema y ramas que representan categorías de causas, permite a los equipos identificar y abordar sistemáticamente las causas raíz de los problemas, mejorando en última instancia los procesos y resultados.
El diagrama de Ishikawa es considerado una de las siete herramientas básicas de control de calidad y se utiliza ampliamente en industrias como la manufactura, la salud y los servicios debido a su efectividad en la identificación de causas raíz y en la mejora de procesos.
La metodología FMEA
El marco de FMEA (Análisis de Modos y Efectos de Falla) anticipa posibles puntos de falla en los procesos y ayuda a mitigarlos.
El Análisis de Modos y Efectos de Falla (FMEA) es un método sistemático para identificar y abordar posibles puntos de falla dentro de un sistema, producto o proceso. Se originó en la década de 1940 y 1950, encontrando un uso significativo en los sectores militar y aeroespacial para anticipar y prevenir posibles fallas en sistemas críticos.
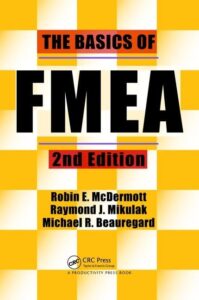
Inicialmente diseñadas para el ejército de los Estados Unidos, los procedimientos para llevar a cabo FMEA fueron descritos en el documento de procedimientos militares MIL-P-1629, con la versión moderna de la práctica codificada en MIL-STD-1629A.
La metodología FMEA evolucionó para incluir elementos cuantitativos como el Número de Prioridad de Riesgo (RPN) en la década de 1970, mejorando su precisión analítica. A medida que los sistemas de gestión de calidad como el Total Quality Management y Six Sigma crecieron en las décadas de 1980 y 1990, FMEA se convirtió en un componente clave de los esfuerzos de mejora continua dentro de las organizaciones.
A lo largo de los años, el FMEA ha sido adoptado por varias industrias, incluyendo la automotriz, donde Ford Motor Company lo utilizó para informar sobre consideraciones de seguridad y regulación, y más tarde el Grupo de Acción de la Industria Automotriz publicó un estándar de FMEA específicamente para la industria automotriz. Hoy en día, industrias que van desde la atención médica hasta el desarrollo de software utilizan FMEA para mitigar riesgos y mejorar la calidad y la seguridad.
FMEA es respaldado por diversas herramientas digitales que proporcionan cálculos de riesgo automatizados y plataformas colaborativas, lo que permite un análisis y reporte eficiente. Estas herramientas y la integración de FMEA con otras técnicas analíticas como el Análisis del Árbol de Fallos (FTA) han mantenido la metodología relevante y adaptable a las necesidades cambiantes de las industrias modernas enfocadas en la fiabilidad, seguridad y excelencia.
Mira las soluciones de Visure que ofrecen perspectivas sobre la evolución de esta herramienta crítica de gestión de riesgos.
La metodología de las 5S
La metodología de las 5S (Ordenar, Organizar, Limpiar, Estandarizar, Sostener) ofrece un enfoque sistemático para organizar el lugar de trabajo que promueve la eficiencia y la efectividad.
La metodología 5S es un enfoque sistemático para la organización y estandarización del lugar de trabajo, originario de Japón y un componente fundamental del sistema de producción lean. Desarrollado en Japón, fue identificado como una de las técnicas que permiten la fabricación justo a tiempo, especialmente en Toyota en la década de 1950.
La exitosa integración de los principios 5S de Toyota en su sistema de producción contribuyó a su ascenso como uno de los principales fabricantes de automóviles y ayudó a difundir la metodología en industrias de todo el mundo.
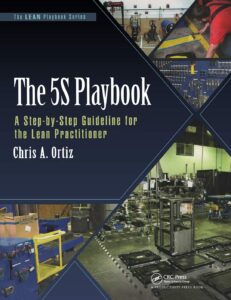
Los principios fundamentales de 5S, conocidos en japonés como seiri (clasificar), seiton (ordenar), seisō (limpiar), seiketsu (estandarizar) y shitsuke (sostener), guían a las organizaciones a mantener un espacio de trabajo limpio, ordenado y bien organizado. Estos pasos tienen como objetivo aumentar la eficiencia, la seguridad y la fluidez del flujo de trabajo en general.
Organizaciones fuera de la manufactura, incluyendo el sector de la salud, educación y venta al por menor, también han adoptado el 5S, encontrando que sus principios apoyan universalmente la eficiencia operativa y una cultura de mejora continua.
Para implementar 5S, las compañías a menudo utilizan auditorías y herramientas de gestión visual para mantener y mejorar el sistema establecido de 5S. Estas auditorías son críticas para garantizar el éxito de la metodología, ya que ayudan a confirmar la comprensión y aplicación adecuada de los principios de 5S. La introducción de la metodología 6S, que incorpora la seguridad como un principio adicional, subraya la adaptabilidad de la metodología y el compromiso de crear entornos de trabajo seguros.
En cuanto a herramientas, varias soluciones de software apoyan la implementación y auditoría de la metodología 5S. Ofrecen características para rastrear el progreso, facilitar la comunicación y garantizar el cumplimiento de los estándares 5S. La digitalización de las prácticas 5S a través de estas herramientas agiliza aún más el proceso e lo integra en las operaciones comerciales modernas.
El uso de 5S, su implementación estructurada y la auditoría continua pueden conducir a una reducción significativa de desperdicios, una mayor productividad y una mejora en la seguridad en el lugar de trabajo. Permite la organización de los espacios físicos y la optimización de los flujos de trabajo en diversos entornos operativos, incluyendo tanto entornos de productos como de servicios (SafetyCulture).
Lean Seis Sigma en la Gestión de Procesos de Negocio (BPM)
En el ámbito de BPM, todos los enfoques de gestión convergen, y Lean Six Sigma se destaca como un impulsor principal de la excelencia en los procesos.
Los profesionales de BPM utilizan Lean Six Sigma para agilizar los flujos de trabajo, eliminar desperdicios y garantizar la calidad, lo cual es esencial en el panorama competitivo de hoy en día.
El Valor para Profesionales
Para los profesionales versados en Lean Six Sigma dentro de BPM, el valor es claro. Poseen la capacidad no solo de mejorar el rendimiento operativo, sino también de generar importantes ahorros financieros y mejoras en la satisfacción del cliente. Estas habilidades están en alta demanda ya que las organizaciones buscan optimizar sus procesos y garantizar la calidad.
¿Listo para mejorar tu carrera y generar un cambio significativo en tu organización? Nuestro curso de BPM Fast Mode te proporcionará las herramientas y el conocimiento para aplicar los principios de Lean Six Sigma de manera efectiva.
Unete a nosotros en BPM Fast Mode y comienza tu camino para convertirte en un campeón de la excelencia en procesos. Tu camino para dominar Lean Six Sigma y transformar los procesos empresariales comienza aquí. ¡Regístrate ahora y sé el profesional que no solo comprende el proceso sino que lo mejora continuamente!